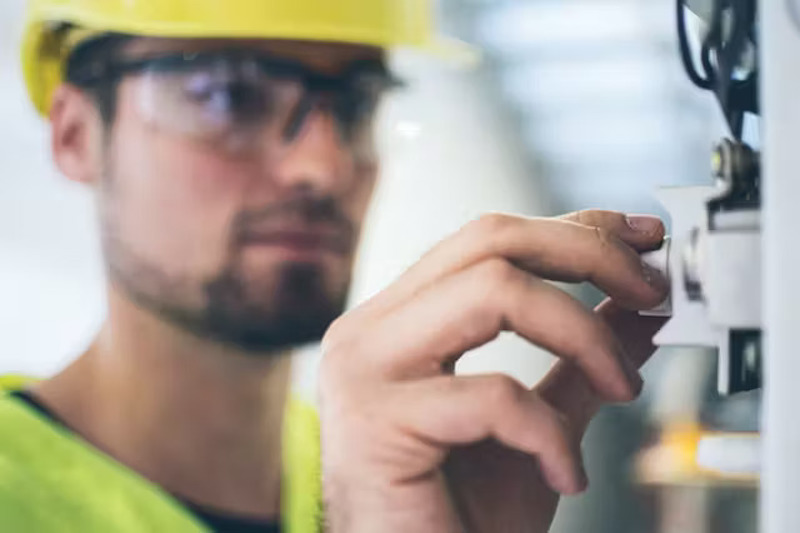
Troubleshooting Motor Control Centers (MCCs): Common Issues and Solutions
Motor Control Centers (MCCs) play a critical role in industrial and commercial settings by managing and controlling the operation of electric motors and other electrical equipment. Like any complex system, MCCs can experience issues that impact performance and disrupt operations. Prompt troubleshooting and resolution of these problems are essential to maintaining efficiency and preventing costly downtime.
This article explores the common challenges faced in MCCs, along with practical troubleshooting strategies. From identifying faulty components to testing electrical connections and implementing preventive maintenance measures, we will cover key techniques to help ensure your MCCs operate smoothly and reliably. By understanding the fundamentals of MCC troubleshooting, you can enhance the longevity and dependability of these essential systems in your facility.
1. Understanding Motor Control Centers (MCCs) and Common Issues
MCCs serve as centralized systems for controlling and distributing electrical power to motors in industrial and commercial environments. They typically consist of multiple motor starters, feeder breakers, and other control devices housed within a single enclosure. Despite their critical role, MCCs are susceptible to a range of problems that can disrupt functionality. Recognizing these issues is the first step toward effective troubleshooting and resolution.
Common MCC Issues and Their Causes
- Electrical Overload
- Occurs when a motor draws more current than its rated capacity, leading to overheating and potential damage.
- Common causes: Mechanical issues in the motor, voltage fluctuations, or improper motor starter sizing.
- Solutions: Inspect connections, verify motor load ratings, and ensure proper starter selection.
- Short Circuits
- Result from faults in the electrical system or malfunctioning components within the MCC.
- Can cause severe damage and pose safety risks.
- Troubleshooting steps: Inspect wiring for damage, test components for faults, and verify protective devices are functioning correctly.
- Motor Starter Failures
- Motor starters control the operation of motors, and any failure can prevent proper motor function.
- Common issues: Contactor failure, overload relay malfunctions, and control circuit problems.
- Solutions: Inspect components for wear, test control circuits for continuity, and adjust overload relays as necessary.
- Insufficient Cooling
- Proper cooling is essential for dissipating heat generated by electrical components and preventing overheating.
- Common causes: Blocked vents, malfunctioning cooling fans, or poor airflow.
- Solutions: Inspect ventilation, clear obstructions, and ensure cooling fans operate correctly.
- Power Supply Issues
- Voltage fluctuations, phase imbalances, or power surges can lead to erratic motor behavior.
- Solutions: Monitor power supply quality, install voltage stabilizers or surge protectors, and ensure a stable power source.
By identifying these common MCC issues early, you can take proactive steps to prevent failures and extend the lifespan of your equipment.
2. Conducting a Thorough Visual Inspection of the MCC
Performing a detailed visual inspection is one of the most effective ways to identify potential MCC issues such as loose connections, overheating, or component wear.
Key Steps in Visual Inspection
- Check for Loose Connections
- Inspect all cables, wires, and terminals to ensure they are tightly secured.
- Look for corrosion or discoloration, which may indicate poor connections.
- Detect Signs of Overheating
- Examine circuit breakers, contactors, and overload relays for signs of heat damage, such as discoloration, melting, or burn marks.
- Listen for unusual noises or check for unusual odors that may indicate overheating.
- Inspect for Physical Damage
- Look for cracks, frayed wires, or damaged insulation on components.
- Ensure screws, bolts, and fasteners are properly secured.
- Evaluate the MCC Enclosure Condition
- Check for signs of rust, water damage, or corrosion that could compromise the enclosure’s integrity.
- Ensure ventilation openings are free of obstructions.
- Document Findings
- Record any identified issues for future reference and maintenance planning.
Regular visual inspections help detect early signs of MCC malfunctions, preventing more serious failures.
3. Utilizing Diagnostic Tools and Techniques
To accurately identify the root cause of MCC issues, various diagnostic tools and methods can be employed.
Essential Diagnostic Tools and Their Functions
- Thermal Imaging
- Identifies hot spots that indicate potential overheating, loose connections, or failing components.
- Current Monitoring
- Detects abnormal fluctuations or excessive current draw, which may indicate short circuits or faulty components.
- Power Quality Analysis
- Monitors voltage stability and identifies fluctuations or disturbances that could affect MCC performance.
- Voltage Testing
- Measures voltage levels at key points in the MCC to detect voltage drops or irregularities.
By leveraging these diagnostic tools, maintenance teams can quickly pinpoint issues and implement necessary corrective actions.
4. Implementing Corrective Actions
Once the root cause of an MCC issue has been identified, appropriate corrective actions must be taken.
Common Corrective Actions
- Tightening Electrical Connections
- Loose connections can lead to poor conductivity and overheating.
- Regularly check and tighten all terminals and connections.
- Replacing Faulty Components
- Components such as contactors, relays, fuses, and circuit breakers degrade over time and require replacement.
- Systematic testing helps identify which parts need replacement.
- Adjusting System Settings
- Fine-tune motor overload settings, voltage levels, and control logic programming to optimize MCC performance.
- Ensuring Safety Compliance
- Always follow proper lockout/tagout procedures before working on MCCs.
- Engage certified electricians for complex repairs.
- Conducting Post-Repair Testing
- After corrective actions are completed, conduct functional and load tests to verify that the MCC is operating correctly.
By systematically addressing issues, you can restore MCC functionality while ensuring long-term reliability.
5. Documenting the Troubleshooting Process and Maintenance Records
Maintaining accurate documentation of troubleshooting efforts and repairs is essential for future reference and preventive maintenance planning.
Key Documentation Practices
- Record Initial Issue Reports
- Note the symptoms, error messages, and observed abnormalities.
- Track Troubleshooting Steps
- Document tests conducted, measurements taken, and findings observed.
- Detail Repairs and Maintenance Actions
- Specify which components were replaced or repaired, along with any modifications made.
- Store Testing Results
- Record the results of post-repair testing to confirm that the issue has been resolved.
- Prepare Summary Reports
- Compile a comprehensive report outlining the troubleshooting and repair process.
Proper documentation improves efficiency in future maintenance tasks and ensures compliance with safety and operational standards.
6. Conclusion
Effective MCC troubleshooting requires a structured approach and a thorough understanding of the system’s components and operation. By employing systematic diagnostic techniques, conducting regular inspections, and implementing appropriate corrective actions, technicians can minimize downtime and maintain optimal performance.
Prioritizing safety and precision throughout the troubleshooting process is crucial in preventing hazards and avoiding costly disruptions. A proactive maintenance strategy, supported by accurate documentation, will enhance the longevity and reliability of your MCC system, ensuring smooth and efficient operations.
Professiona Switchgear supplier and manufacturer
- Zhejiang GONGSHUN Electrical Co.,Ltd (electricgs.com), Our company was founded in the late 1990s, specializing in the production of inflatable cabinets, SF6 inflatable cabinets, and various high and low voltage complete sets of electrical equipment. It has multiple subsidiaries under its jurisdiction, including high-voltage load switch branch, high-voltage circuit breaker branch, high-voltage fuse branch, and technology development branch.Our technical expertise, comprehensive product portfolio and long-term rich experience are helping many customers in need to solve their power problems. We’re happy to help at any time. Whether you need application product advice or technical assistance, our global service team is committed to providing you with the right support. For more technical information about medium voltage earthing switch, feel free to contact us, send an email to gongshun@electric-cn.com
- Our company specializes in producing 12KV-40.5KV series high-voltage electrical products: FZN58, FLN48, FLN36, FZRN25, FZN21, FN18, ZFN16, FN12, FN8, FN7, FN5, XRNT, XRNP, VS1, ZN28, ZW8, ZW32, JN15, GN19, GN22, GN24, GN30, CLXGN15-12, HXGN □ -12, DXG-12 (L), DFW □ -12 high-voltage cable branch box, CLXGN □ -12 (SF6) series inflatable cabinet 12KV and 35KV cable accessories, etc; CLVXP-12 indoor AC high voltage fixed switchgear, CL-SIS-12 compact solid insulated ring main unit, professional assembly Schneider SC6 (SF6) series load switchgear, ABB produced SFG (SF6) series load switchgear and other series products; Distribution and agency of high-voltage load switches and inflatable cabinets produced by Schneider Electric and ABB; Siemens produces the 3AJ1 series of indoor medium voltage vacuum circuit breakers and other related products. The company has a complete range of products and has been operating safely on domestic and international power grids for a long time, receiving unanimous praise from both new and old users. Among them, multiple products such as FZRN25, FN12, FLN36-12, XRNT-12 have been exported to various countries and regions in East Asia, South Asia, Southeast Asia, Africa, and the United States.