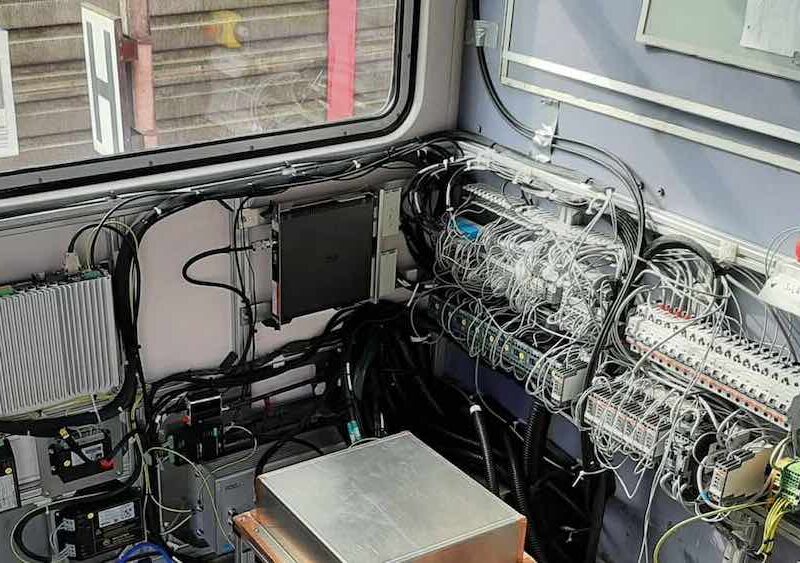
Industrial I/O Modules: Comparison and Application of Local and Remote I/O
Industrial I/O (Input/Output) modules are critical components in industrial networks. They transmit input signals from field devices such as sensors or actuators to the controller and relay output commands from the controller back to these devices. Initially, I/O was directly connected to the PLC (Programmable Logic Controller) CPU or expanded through additional modules attached to the CPU. However, as industrial automation evolved and factories expanded, some I/O devices were installed at remote locations, making traditional expansion methods impractical due to complex wiring and maintenance challenges.
To address these issues, Remote I/O and Distributed I/O emerged, allowing I/O modules to be installed in strategic locations while communicating with the PLC over a network. While the concept may seem straightforward, choosing the right I/O deployment strategy requires a clear understanding of Local, Remote, and Distributed I/O to ensure system reliability and efficiency.
1. Types of Industrial I/O
In PLC systems, I/O modules are typically categorized into three types:
- Local I/O – Directly connected to the controller, usually housed in the same cabinet.
- Remote I/O – Installed away from the main controller and communicates via a network.
- Distributed I/O – A more advanced version of remote I/O with processing capabilities that allow localized decision-making.
1) Local I/O
Local I/O refers to input and output modules that are physically close to the PLC controller and directly connected to it via an integrated chassis or rack. These I/O modules are typically supplied by the same manufacturer as the PLC and come in configurations supporting 4, 8, 16, or 32 I/O points.
Key Features:
- Fast response time due to direct connection with the controller, minimizing signal delay.
- Best suited for small control systems, particularly when the I/O devices are within close proximity to the control panel.
- Limited scalability – If the system requires additional I/O points at distant locations, signal degradation and wiring complexity can become major concerns.
2) Remote I/O
Remote I/O addresses the distance limitation of local I/O. Imagine a scenario where multiple I/O clusters exist at distant locations, such as different sections of a factory. These I/O groups can be connected to remote racks, which communicate with the PLC through a network adapter using EtherNet/IP, Modbus TCP/IP, Profibus, Profinet, or other industrial protocols.
Advantages of Remote I/O:
- Reduces wiring complexity – Instead of running multiple individual wires from each sensor to the PLC, remote I/O enables communication over a single network cable.
- Increases installation flexibility – I/O modules can be placed closer to machines, reducing long cable runs.
- Ensures reliable communication – Modern network protocols provide high-speed data transfer and low signal loss.
In a remote I/O system, the network infrastructure plays a crucial role in ensuring efficient and reliable data transmission between the CPU and field devices. The network must be robust enough to handle high data traffic and harsh industrial conditions while maintaining low error rates.
3) Distributed I/O
Distributed I/O is an enhanced version of remote I/O. The primary difference is that each remote rack has its own processor (CPU), allowing it to process certain tasks independently from the main PLC.
Characteristics of Distributed I/O:
- Each remote unit has processing capability, reducing the burden on the main PLC.
- Ideal for large-scale automation systems, where multiple control points require decentralized processing.
- Improves system scalability and fault tolerance, as each distributed controller can operate independently in case of communication failure.
While many automation vendors use Remote I/O and Distributed I/O interchangeably, the key distinction is that Distributed I/O includes intelligent processing, while Remote I/O simply acts as an extension of the main PLC.
2. Local vs. Remote I/O: Key Differences
When deciding between Local I/O and Remote I/O, several key factors should be considered:
1) Distance
- Local I/O is located near the main PLC, which limits installation flexibility.
- Remote I/O can be placed at a distance from the PLC, allowing greater design flexibility in large or complex industrial facilities.
2) Wiring
- Local I/O requires direct wiring to the PLC, which can result in complex and cluttered wiring as the system expands.
- Remote I/O significantly reduces wiring requirements by using a network-based communication system.
3) Reliability
- Local I/O provides instantaneous communication with the PLC, ensuring minimal signal delay.
- Modern Remote I/O networks are highly reliable, with low latency and robust error handling mechanisms.
4) Maintenance
- Local I/O is easier to maintain initially because all devices are centralized. However, as the system scales, troubleshooting becomes more complex.
- Remote I/O follows a modular approach, making it easier to diagnose and replace faulty components without disrupting the entire system.
5) Cost
- Local I/O has a lower initial cost but becomes expensive as the system grows due to increased wiring and installation costs.
- Remote I/O provides long-term cost savings by minimizing cable requirements and simplifying system expansion.
3. The Role of I/O Modules in Industrial Networks
Historically, Direct Digital Control (DDC) systems were the predecessors of DCS (Distributed Control System) and PLCs. Early industrial control relied on large centralized computing systems that struggled with slow data transmission and limited scalability. Today, modern I/O modules play a crucial role in efficient industrial automation by streamlining data exchange between PLCs and field devices.
Functions of I/O Modules:
- Convert digital signals from the PLC into electrical signals for output devices (actuators, motors, valves).
- Convert electrical signals from input devices (sensors, switches) into digital signals for the PLC.
- Ensure smooth data transmission by buffering and pre-processing signals, reducing CPU workload.
- Improve system modularity, allowing flexible system expansion based on operational needs.
The design and complexity of I/O modules vary depending on system requirements. Some basic modules handle only digital signals, while others process analog data, temperature readings, or even perform advanced diagnostics.
4. Conclusion
Both Local I/O and Remote I/O play critical roles in industrial automation, each with its own strengths and trade-offs.
- Local I/O is ideal for applications requiring high-speed signal processing and minimal delay but is limited in scalability.
- Remote I/O is better suited for large-scale systems, offering cost-effective wiring, greater flexibility, and easier expansion.
- Distributed I/O takes it a step further by providing autonomous processing power, reducing the burden on the main PLC.
Choosing the right I/O deployment strategy depends on operational requirements, system complexity, and long-term scalability needs. By understanding the fundamental differences between local and remote I/O, engineers can design more efficient, scalable, and reliable industrial automation systems.
Professiona Switchgear supplier and manufacturer
- Zhejiang GONGSHUN Electrical Co.,Ltd (electricgs.com), Our company was founded in the late 1990s, specializing in the production of inflatable cabinets, SF6 inflatable cabinets, and various high and low voltage complete sets of electrical equipment. It has multiple subsidiaries under its jurisdiction, including high-voltage load switch branch, high-voltage circuit breaker branch, high-voltage fuse branch, and technology development branch.Our technical expertise, comprehensive product portfolio and long-term rich experience are helping many customers in need to solve their power problems. We’re happy to help at any time. Whether you need application product advice or technical assistance, our global service team is committed to providing you with the right support. For more technical information about medium voltage earthing switch, feel free to contact us, send an email to gongshun@electric-cn.com
- Our company specializes in producing 12KV-40.5KV series high-voltage electrical products: FZN58, FLN48, FLN36, FZRN25, FZN21, FN18, ZFN16, FN12, FN8, FN7, FN5, XRNT, XRNP, VS1, ZN28, ZW8, ZW32, JN15, GN19, GN22, GN24, GN30, CLXGN15-12, HXGN □ -12, DXG-12 (L), DFW □ -12 high-voltage cable branch box, CLXGN □ -12 (SF6) series inflatable cabinet 12KV and 35KV cable accessories, etc; CLVXP-12 indoor AC high voltage fixed switchgear, CL-SIS-12 compact solid insulated ring main unit, professional assembly Schneider SC6 (SF6) series load switchgear, ABB produced SFG (SF6) series load switchgear and other series products; Distribution and agency of high-voltage load switches and inflatable cabinets produced by Schneider Electric and ABB; Siemens produces the 3AJ1 series of indoor medium voltage vacuum circuit breakers and other related products. The company has a complete range of products and has been operating safely on domestic and international power grids for a long time, receiving unanimous praise from both new and old users. Among them, multiple products such as FZRN25, FN12, FLN36-12, XRNT-12 have been exported to various countries and regions in East Asia, South Asia, Southeast Asia, Africa, and the United States.